Executive Summary
The edible oil market enjoys high competition, and companies rely on strong packaging when it comes to product integrity, faster transportation, and customer satisfaction. This client, which leads in edible oil tin manufacturing with a wide variety of products, wanted to improve their operational efficiency without compromising quality. However, their existing production facility was not capable of meeting the rising demand. Therefore, they focused on maximizing workforce utilization and removing inefficiencies in routine operations.
To overcome such challenges, the company joined forces with Production Modeling India (PMI) to design systematic process improvements. Through methods like PMTS (MODAPTS), optimum work distribution, line balancing, and value stream analysis, the project sought to attain remarkable gains in productivity. The outcome was an optimized operation that could respond to changing customer demands while maintaining optimum utilization of resources.
Issues Faced by Client
Despite its sound infrastructure and seasoned labor force, the client was plagued with multiple operational inefficiencies:
• Work Content Estimation: There was no clear vision for actual work content, and hence assessments of installed production capacity were inaccurate. • Inefficient Work Distribution: Manpower was not optimally allocated across lines, resulting in labor underutilization and uneven throughput. • Balancing Demand with Supply: The company operated multiple tin making and filling lines, each influenced by highly variable demand, making production planning reactive rather than proactive. • Hidden Inefficiencies: Indirect operations contained several Non-Value-Added (NVA) activities that were not well-documented or controlled.These issues limited scalability, increased operational costs, and impacted overall plant productivity.
PMI’s Structured Approach
PMI entered the project with a holistic framework to evaluate, analyze, and enhance the client operations. The subsequent stages were carried out:
1. Scope Definition and Kick-off
A combined team of PMI professionals and client stakeholders was established for the scope definition, describing objectives, and establishing priority areas. The primary aim was to maximize line efficiency and manpower output while developing a system that can adapt to fluctuating production needs.
2. Data Collection and Process Observation
PMI’s team visited the production facility to conduct a thorough assessment of processes. Activities included:
• Video shooting of tin manufacturing and filling processes across different lines.
• Collection of historical data including production volumes, shift timings, and layout drawings.
• Study of existing process flows and operator movements.
3. Elemental Analysis with PMTS (MODAPTS®)
Based on the captured video data, PMI performed a detailed time-motion study applying the MODAPTS technique. The tasks were dissected into basic operations and time standards allocated.
This facilitated:
• Precise estimation of work content for every process step.
• Value-added vs. non-value-added activity identification.
• Clarity of visibility into manpower workloads and machine cycles.
4. Work Distribution & Line Balancing
Using validated time information, PMI designed man-machine charts to examine workloads and resource interactions. Emphasis was laid on two cycle time objectives:
• 2.4 seconds (25 tins/min)
• 3.0 seconds (20 tins/min)
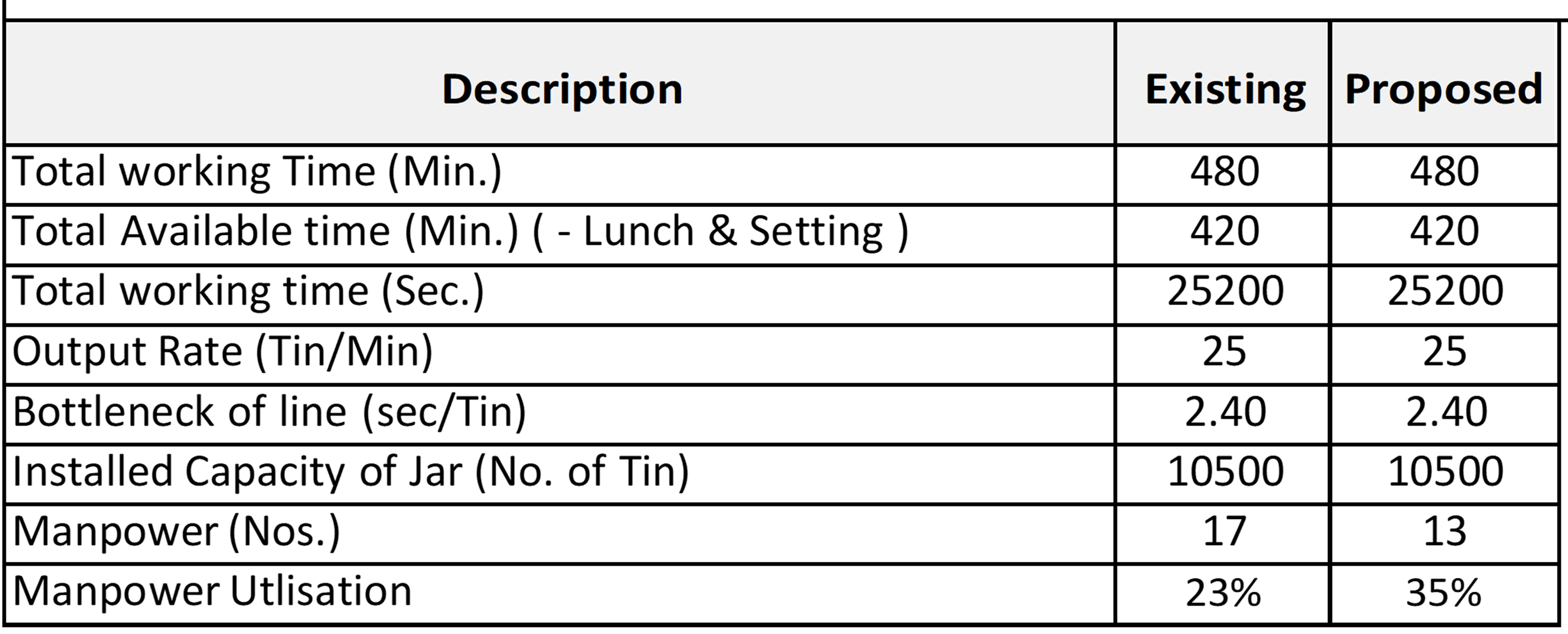
The distribution of work was reorganized to correspond to these objectives, minimizing labor and equipment waste. Overloaded and underloaded workstations were realigned to develop equitable workflows, minimize bottlenecks, and eliminate waste.
5. Layout Improvement and Waste Elimination
Observations from the time study indicated ergonomic inefficiencies and layout defects. PMI recommended:
• Restructuring of the layout for more efficient material flow.
• Suggestions for removal or automation of redundant NVA operations.
Proposals for slight modification of equipment to enhance accessibility and minimize operator fatigue.
Expected Bottlenecks
Data Collection & Joint Validation
During the project, PMI focused on working jointly with the client's internal team. This entailed:
• Discussing elemental breakdowns and time values with operators and supervisors.
• Verification with on-ground observation.
• Training client teams on man-machine chart interpretation and application of MODAPTS data.
By involving the client at every stage, PMI did not only achieve accuracy but ensured ownership of suggested changes as well.
Optimizing Production Efficiency and Workforce Utilization in Edible Oil Tin Manufacturing Industry
Solutions & Strategic Recommendations
PMI introduced the client with a range of actionable solutions:
• Work Distribution Optimization: Refining role distribution to every station so that all operators were fully utilized across many lines.
• Dynamic Dashboard for Production Planning: A tailored dashboard was created to model production output and resource requirements based on fluctuating demand. This instrument facilitated planning workforce and machine allocation effectively.
• Capacity-based Scheduling: Computed maximum possible achievable throughput per line, assisting the client in aligning production with real market demands.
• Waste Removal & Layout Adjustments: Physical changes to layout were suggested to decrease operator paths, minimize handling, and facilitate more coordination between upstream and downstream activities.
Results & Impact
The client indicated post-implementation following benefits:
• 15–18% increase in the utilization of manpower on major lines.
• Smooth tin making and filling line alignment minimized interdependencies.
• Improved flexibility in production scheduling through the use of the interactive dashboard.
• Boosted throughput through decreased process variability.
• Improved in-house capability in sustainable continuous improvement.
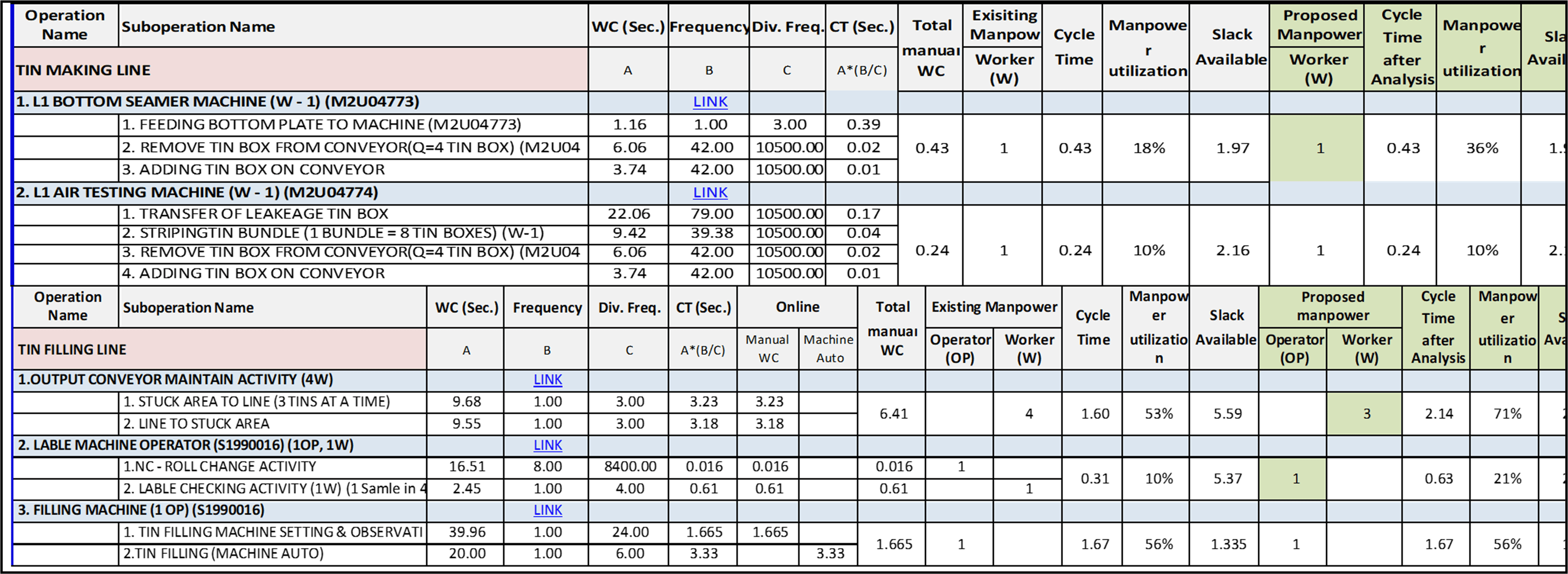
The transformation not only optimized current operations but also provided the foundation for scalable growth in response to fluctuating market needs.
Conclusion
This case study demonstrates how structured process engineering, rooted in PMTS analysis and work balancing, can yield measurable improvements in complex manufacturing environments. PMI’s end-to-end engagement, combining diagnostic expertise with practical solutions, enabled the client to unlock latent potential in its operations.
Whether they are dealing with dynamic demand, underutilized labor, or unbalanced workflows, edible oil tin makers and other companies can copy this model for driving operational excellence and enhancing bottom-line results.