Lean Manufacturing: Your Path to Efficiency and Profitability!
We make manufacturing smarter, faster, and more efficient at PMI. Our Lean Manufacturing Consulting services enable companies to streamline operations, eliminate waste, and increase productivity through time-tested lean management techniques.
With over 30 years of hands-on experience, our expert lean consultants consult with you to find areas of inefficiency, implement 5S Lean Manufacturing, and optimize processes for optimal output. Whether you need to enhance lean material control, eliminate the 8 wastes of Lean Manufacturing, or optimize Six Sigma inventory control, we have the methodology and expertise to assist.
From Lean Six Sigma for service industries to Lean waste management, our customized lean solutions drive measurable outcomes that directly affect your bottom line. Let’s revamp your operations using the power of Lean Management and Six Sigma!
Our Lean Manufacturing Consulting Services Include
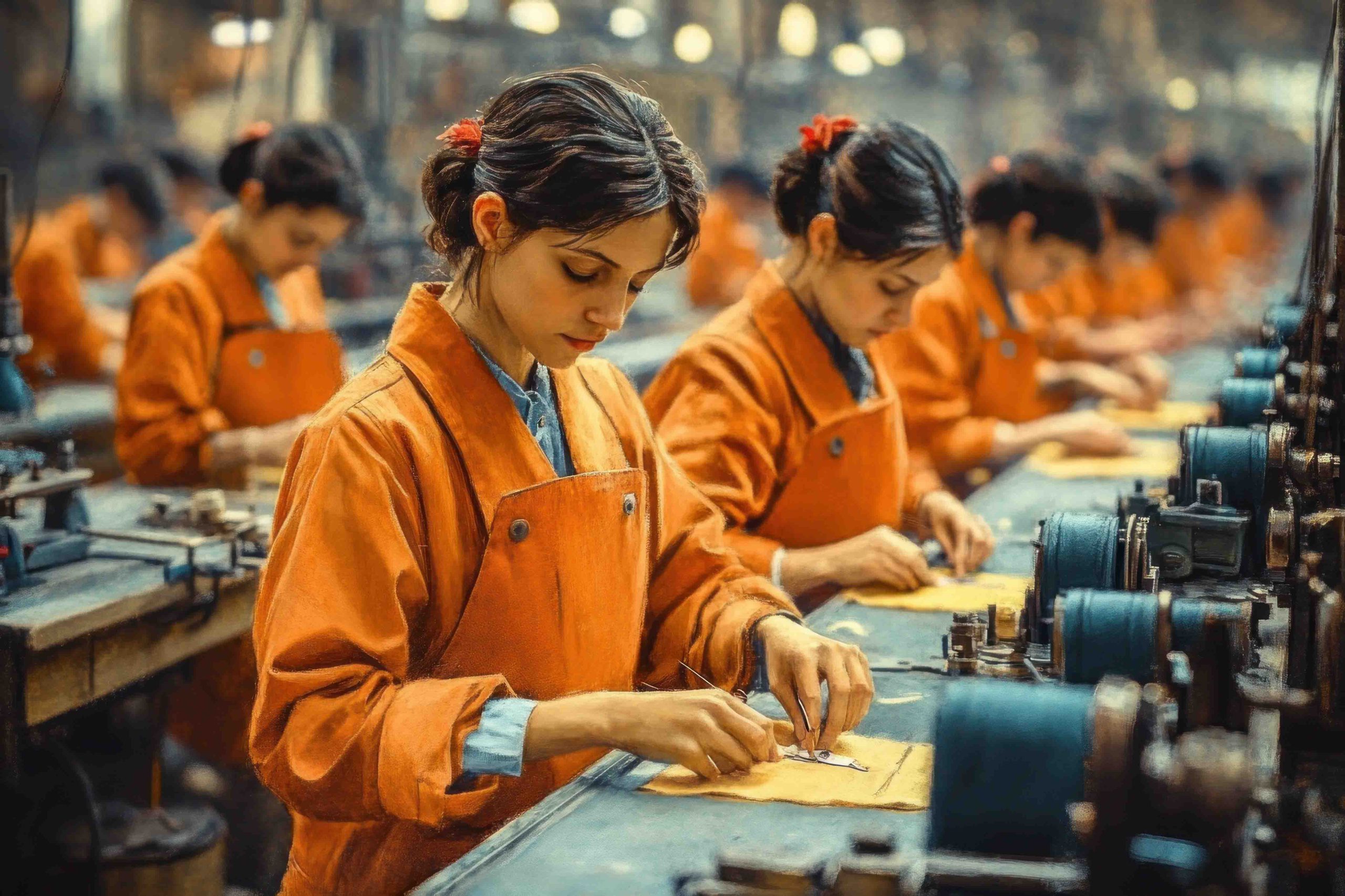
Throughput Analysis
- PMI identifies and removes bottlenecks to increase production output.
- We analyze material flow, process constraints, and task completion time.
- Our recommendations optimize throughput and efficiency across production lines.
- Improved flow leads to higher productivity and reduces operational waste.
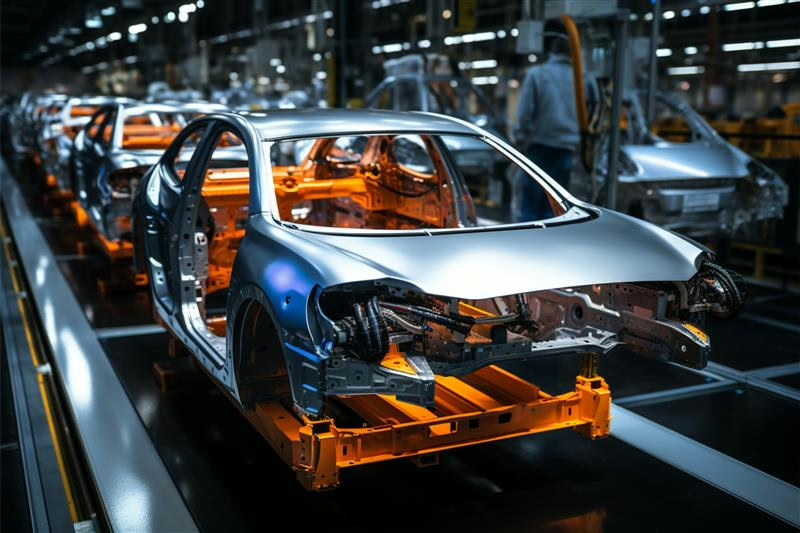
Line Balancing Consulting Services
- We ensure even workload distribution among employees and machines.
- Our line balancing analysis identifies optimal staffing and machine allocation to prevent downtime.
- The goal is to achieve a smooth production flow and maximize capacity.
- Well-balanced assembly lines lead to higher efficiency and reduce operational delays.
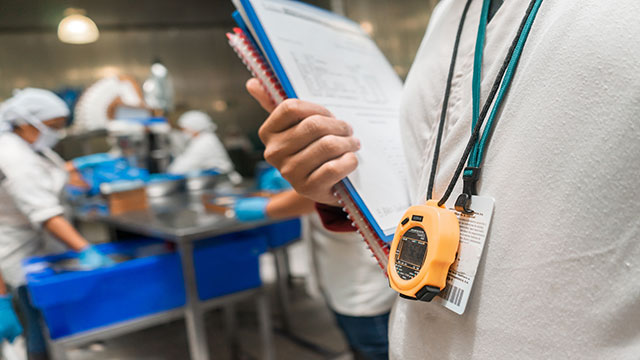
Work Measurement Consulting
- PMI uses time studies, motion studies, and work sampling to optimize productivity.
- We measure time and effort for tasks, identifying inefficiencies and waste.
- Our insights help businesses improve workflow, reduce costs, and enhance efficiency.
- Accurate work measurement leads to better resource allocation and streamlined operations.
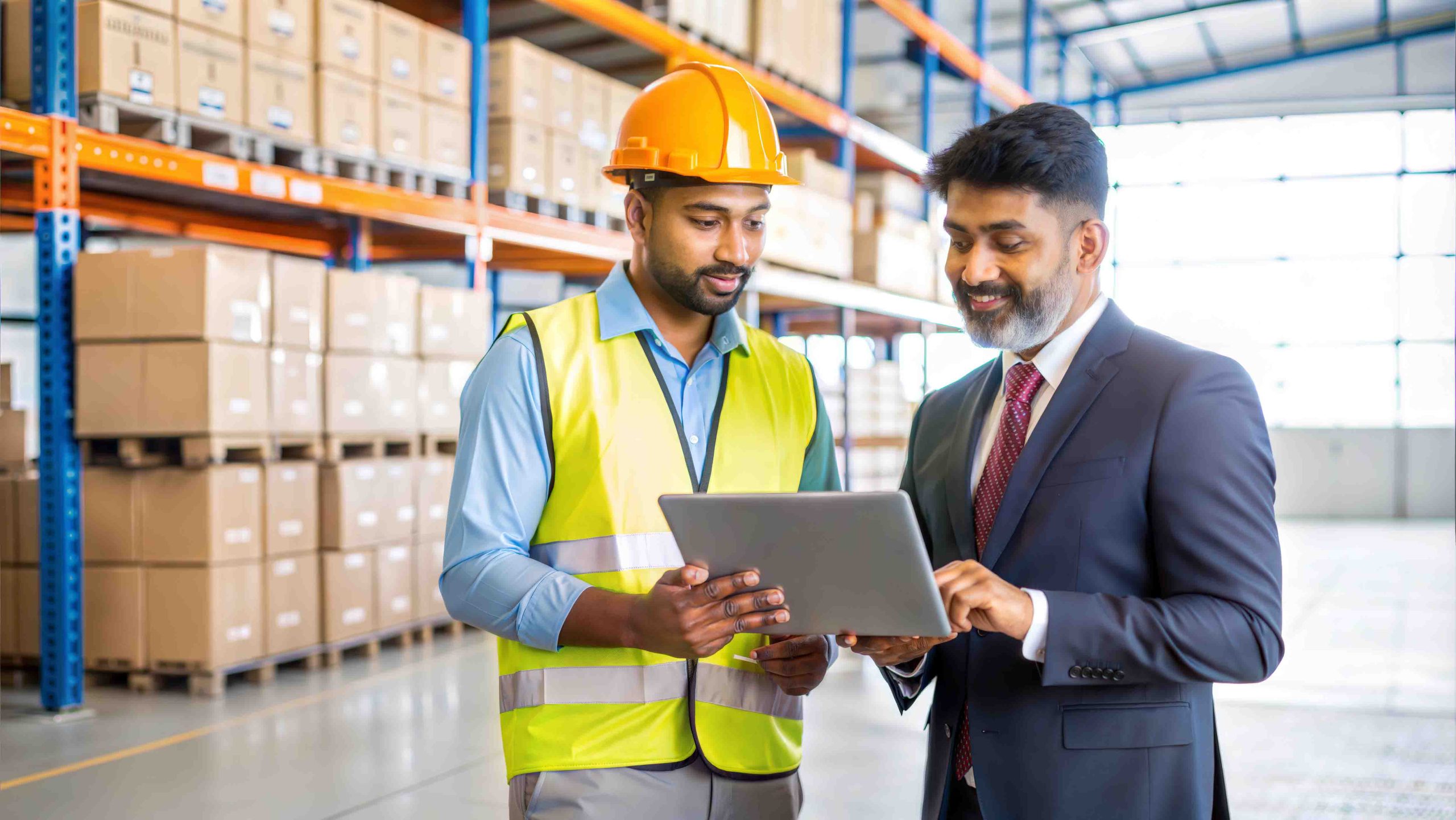
Advanced Production Scheduling
- PMI optimizes production scheduling and resource allocation to boost efficiency.
- We use constraint-based scheduling, simulation modeling, and real-time data analysis for accuracy.
- Our techniques consider production capacity, machine availability, and material flow.
- We provide software recommendations to enhance scheduling and minimize delays.
Want to improve your productivity and efficiency?
Optimize your operations and boost efficiency with our expert Lean Manufacturing Consulting services.
Contact us today to identify hidden inefficiencies and streamline your workflow for maximum productivity!
Industries that Benefit from Lean Manufacturing Consulting
Automotive Manufacturing
Logistics & Supply Chain
Telecommunications
Warehouse & Logistics
Aerospace
Architecture, Engineering, & Construction
Industrial Manufacturing
Energy and Utilities
Engineering
Food and Beverage
Renewables, Oil, and Gas
Construction
Healthcare and Hospitals
Retail
5S System
PMI’s Lean Manufacturing Services include the 5S methodology, a proven system to create an organized, efficient, and waste-free workplace. By implementing Sort, Set in Order, Shine, Standardize, and Sustain, we help businesses reduce downtime, improve workflow, and boost productivity.
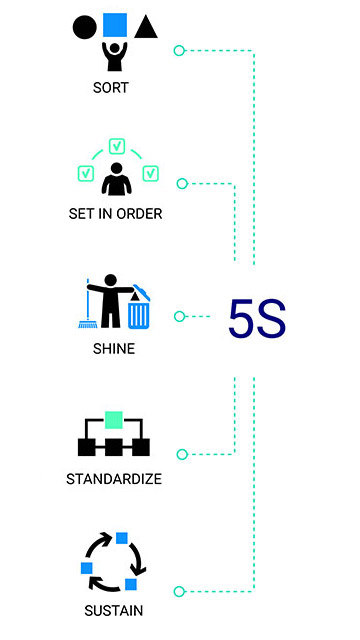
How 5S Works
Sort
Remove unnecessary items, keeping only what’s essential for operations.
Set in Order
Arrange tools and materials in a logical manner to improve accessibility and workflow.
Shine
Ensure cleanliness to avoid defects, detect problems early, and provide a safe environment.
Standardize
Create explicit standards for the maintenance of organization and cleanliness.
Sustain
Regularly monitor and improve practices to maintain efficiency over the long term.
MUDA: Waste – MURA: Irregularity – MURI: Overburden:
PMI’s Lean Manufacturing Services utilize the Muda, Mura, and Muri principles—developed by Toyota—to detect inefficiencies, maximize processes, and maximize productivity. By reviewing production time, losses, and value-added activity, we assist organizations in eliminating waste and minimizing waste.
Understanding the Three M’s:
Muda (Waste)
Any non-value-added activity that hinders efficiency. The 8 types of waste include: Transportation, Inventory, Motion, Waiting, Processing, Overproduction, Defects, and Underutilized Workers.
Mura (Irregularity)
Fluctuations in workflow, demand, or production that lead to inefficiencies.
Muri (Overburden)
Overloading the workers, machines, or processes, leading to breakdowns and inefficiencies.
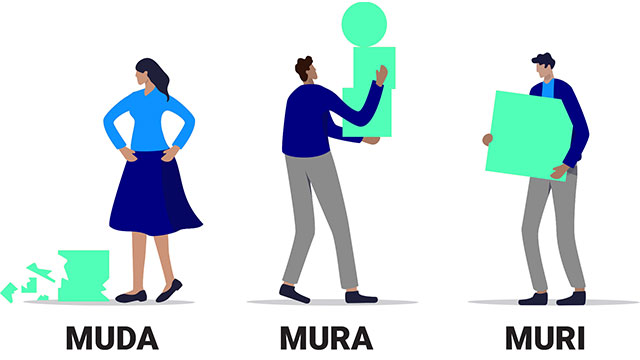
By recognizing Mura (variation) and Muri (overburden), companies can efficiently eliminate Muda (waste)—leaner, more productive operations. Join forces with PMI to streamline your processes and realize operational excellence!
Our Lean Manufacturing Expert
At PMI, our lean manufacturing expert and highly qualified team of lean specialists offers approximately two decades of in-depth experience in Lean Manufacturing Consulting to businesses of various industries with the aim to streamline operations, minimize waste, and increase efficiency. We focus on delivering custom Lean strategies best suited to address your specific business challenges and industry requirements. Our team is dedicated to:
- Determining and choosing the most efficient Lean methods in relation to your precise challenges.
- Implementing industry-leading best practices for process optimization and maximum efficiency.
- Delivering insightful analysis and concrete recommendations to maximize productivity and operations performance.
Together with PMI, you get a reliable partner committed to producing quantifiable outcomes through Lean Manufacturing excellence.
Training on Industrial Engineering Concepts/Techniques and Methodology
PMI offers a variety of Industrial Engineering training courses. From Six Sigma, Lean Manufacturing Techniques, 8S Core Courses, and beyond, PMI can help you enhance your organization’s manufacturing capabilities and drive operational excellence with our comprehensive courses.
These courses offer you specialized knowledge and experience in industrial engineering with best practices and the latest techniques in the field
-
Expertise Specialized knowledge and experience in industrial engineering provide your employees with the latest techniques and best practices in the field.
-
Tailored Solutions Conduct an analysis of your organization's operations and provide tailored training solutions. This can help your organization to achieve its unique goals and objectives.
-
Implementation Support Training alone is not enough! We can provide support in implementation which will ensure that learned techniques drive effective changes.
-
Long-term Benefits Implementing industrial engineering solutions can lead to improvements in productivity, efficiency, and profitability.
Frequently Asked Questions
Lean Manufacturing is a systematic approach aimed at minimizing waste without sacrificing productivity. It focuses on delivering value to the customer by optimizing processes, reducing inefficiencies, and continuously improving operations.
Engaging in Lean Manufacturing Consulting can lead to:
• Enhanced operational efficiency.
• Reduced production costs.
• Improved product quality.
• Shortened lead times.
• Increased customer satisfaction.
By identifying and eliminating non-value-added activities, organizations can achieve streamlined processes and better resource utilization.
Lean principles are versatile and can be applied across various sectors, including:
• Automotive Manufacturing
• Warehouse and Logistics
• Industrial Manufacturing
• Food and Beverage
• Healthcare and Hospitals
• Aerospace
• Energy and Utilities
• Retail
• Telecommunications
• Architecture, Engineering, and Construction
Key tools and methodologies include:
• 5S Methodology: Organizing the workplace for efficiency and effectiveness.
• Kaizen: Continuous improvement through small, incremental changes.
• Value Stream Mapping: Visualizing processes to identify waste.
• Just-In-Time (JIT): Producing only what is needed when it's needed.
• Kanban: Visual scheduling system to manage work.
While both aim to improve processes, Lean focuses on eliminating waste and improving flow, whereas Six Sigma emphasizes reducing variation and enhancing quality through statistical analysis. Combining both approaches, known as Lean Six Sigma, can provide comprehensive process improvement.
A Lean Manufacturing Consultant assists organizations in:
• Assessing current processes.
• Identifying areas of waste and inefficiency.
• Implementing Lean tools and techniques.
• Training employees on Lean principles.
• Ensuring sustainable continuous improvement.
The timeframe varies based on the organization's size, complexity, and commitment. Some improvements can be observed within weeks, while a full cultural transformation may take months to years.
Absolutely. Lean principles are applicable to various sectors beyond manufacturing, including healthcare, finance, and service industries, by focusing on process efficiency and waste reduction.
The 5S methodology stands for Sort, Set in order, Shine, Standardize, and Sustain. It's a foundational Lean tool that promotes workplace organization, cleanliness, and standardization, leading to improved efficiency and safety.
Initiating Lean Manufacturing Consulting involves:
• Conducting a comprehensive assessment of current processes.
• Identifying key areas for improvement.
• Developing a tailored Lean implementation plan.
• Engaging employees through training and involvement.
• Monitoring progress and making iterative improvements.
Collaborating with experienced consultants can guide your organization through this transformative journey.
Want to schedule a time to speak with one of our Lean Manufacturing Consulting Consulting representatives now?
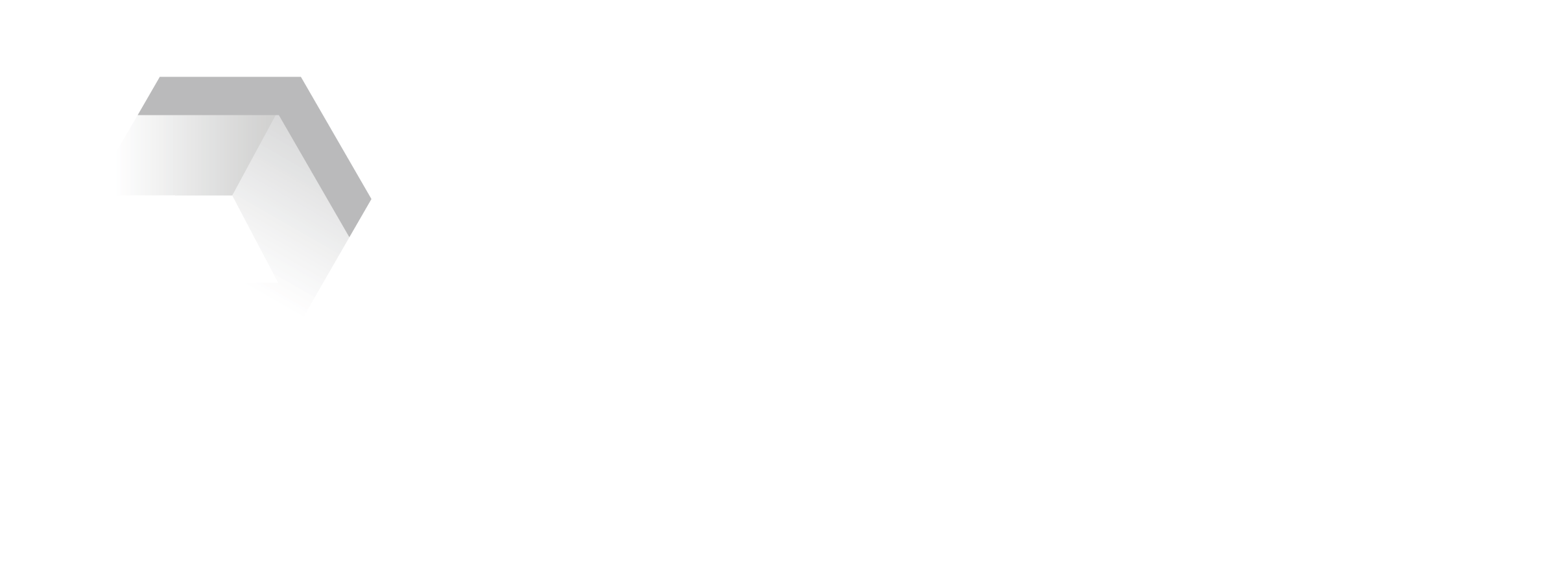
Let our experts show you how our Services can support your projects!
Send a message to our team by filling out the form below. Describe your project, ask questions, or even request a bid.
An expert from our team will be in touch with you within one business day!