Introduction
In today's fast-changing energy industry, producers of high-performance electrical components need to innovate constantly not only in product development but also in their business. The case study showcases the journey of transformation of a renowned manufacturer and supplier of a wide range of energy infrastructure products—from cable connection systems and asset protection products to heat tracing solutions and electrical safety solutions.
Spurred by a desire to provide innovative, reliable, and efficient solutions to the world energy infrastructure market, the company allied with Production Modeling India (PMI) to rationalize its operations across multiple production lines. With the integration of PMTS methods, man-machine optimization, and NVA elimination, the client experienced a remarkable leap in operational efficiency, labor productivity, and equipment utilization.
Client Profile and Project Background
Although possessing an evolved product portfolio and strong market share, the client was confronting a number of operational challenges affecting overall productivity:
• Man and machine mismatch on three principal production lines. • Inadequate work content measurement through standardized work, resulting in variable outputs • Low levels of manpower utilization and unstated station capacities. • Existence of NVA activities both in manual and machine operations. • Lack of systematic methodology to resource planning and performance benchmarking.These inefficiencies were limiting throughput, increasing idle time, and reducing the effectiveness of both human and capital resources. The client was in search of a systematic, data-driven strategy to align its operational framework with its strategic goals.
PMI’s Structured Approach
PMI initiated the engagement with a collaborative spirit, working closely with the client’s cross-functional team to define scope, map processes, and build a unified understanding of the manufacturing setup.
1. On-Site Observation and Video Recording
Our team went to the client's factory site to:
• Observe existing operations in real time.
• Gain an understanding of task sequencing, flow, and resource interdependencies.
• Capture extensive video recordings of machine-based and manual activities for every one of the three lines under consideration.
2. Work Content Measurement using PMTS
We used the MODAPTS (Modular Arrangement of Predetermined Time Standards) method, an established PMTS technique, to:
• De-aggregate each observed activity into atomic components.
• Allocate standardized time values to each element in order to calculate work content.
• Detect inefficiencies and time wastage through a micro-level examination.
3. Concurrent Validation
Both elemental job task analysis and time estimates were communicated to the client for concurrent validation. This guaranteed:
• Openness in data treatment.
• Process-specific information from client-side specialists.
• Early acceptance for forthcoming recommendations and suggested modifications.
4. Manpower Usage and Balancing
On the basis of validated work content:
• Actual vs. optimum manpower utilization across stations was calculated.
• Mapped workload allocation to available capacity.
• Created optimized balancing plans that minimize idle time and maximize throughput.
Data Collection & Process Understanding
One of the key success factors in this project was our comprehensive data collection process. Along with video, our team:
• Worked with the client's Cross Functional Team (CFT) to achieve detailed knowledge of workflows and constraints.
• Mapped machine cycle times, setup, and ergonomic restrictions.
• Made side-by-side comparisons of high-performing and underperforming stations.
• The map identified fatigue-prone areas and inefficient movements that were consuming productivity.
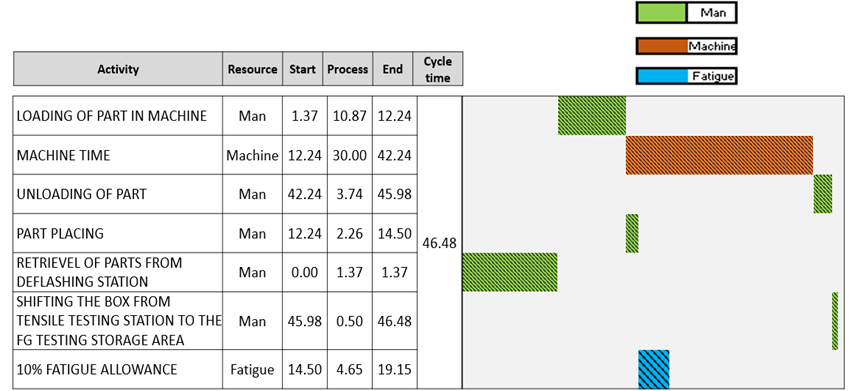
The outcome was a rich, validated dataset that allowed us to map actual work content to actual execution times—setting the stage for effective improvement planning.
Production Analysis in Car Manufacturing Industry - Case Study
Recommendations and Proposed Solutions
After analysis, PMI created three proposed scenarios with different intervention levels:
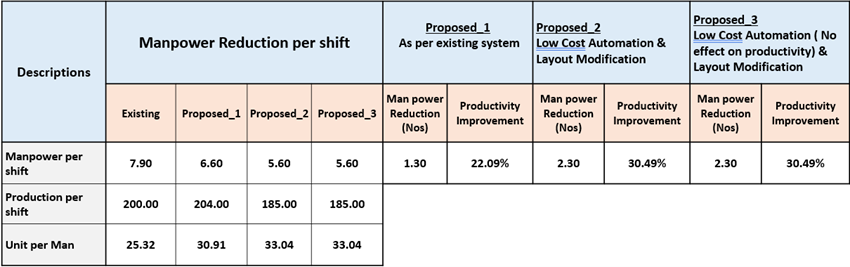
1. Base Optimization
• Improved operator movements and minimized waiting time.
• Reassigned tasks to enhance load sharing.
• Suggested simple workflow changes without any need for capital outlay.
2. Intermediate Adjustment
• Small layout modifications to facilitate more efficient workpiece transfer.
• Recommended tooling upgrades to reduce cycle times.
• With an emphasis on ergonomics and reducing fatigue.
3. Strategic Overhaul
• Planned major re-balancing of manpower and machines between lines.
• Determined NVA-burdened activities for automation or elimination.
• Developed a plan for future digital work standard implementation based on PMTS data as a basis.
Existing Layout
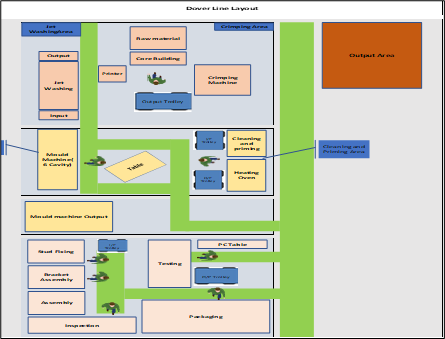
Proposed Layout
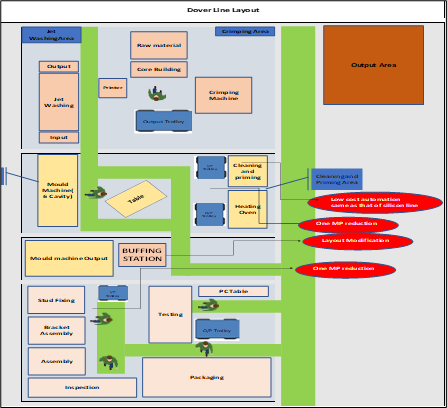
Each scenario had with it projected manpower savings, increased utilization percentages, and cycle time estimates.
Results & Measurable Impact
As a result of PMI’s engagement, the client achieved the following improvements:
• Manpower utilization increased by 15–20% across critical stations.
• Machine downtime was reduced through better planning and synchronized workflows.
• Identification and elimination of NVA activities led to a 5–7% productivity gain.
• Clear visibility into maximum station capacity, enabling informed production planning.
• Established work content benchmarks for future process monitoring and training.
These gains enabled the client to synchronize its capacity for production with growing market demand—without costly capital investment.
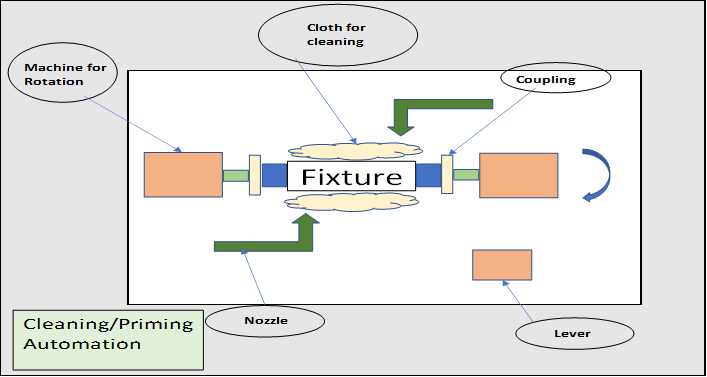
Potential Improvements
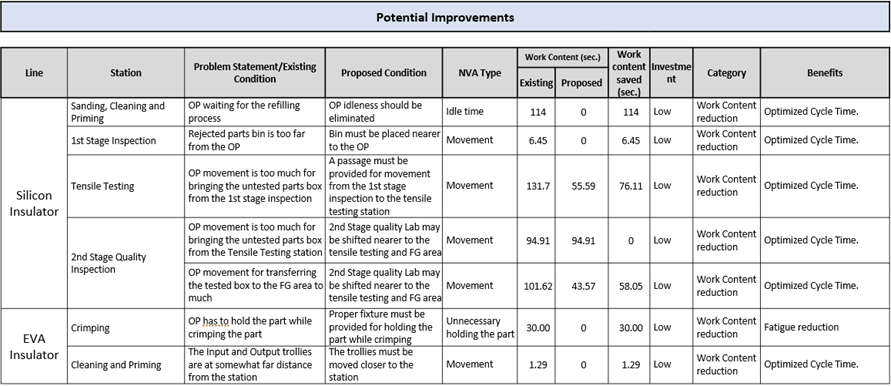
Conclusion & Strategic Takeaway
This case illustrates how a scientific and systematic approach to work measurement and resource balancing can unlock great value in factory operations. The use of PMTS by PMI, supplemented by hands-on process analysis and participative involvement, facilitated the client's approach to its vision of operational excellence.
By eliminating guesswork and basing decisions on data-driven recommendations, energy infrastructure manufacturers can not only enhance day-to-day effectiveness, but also establish a solid foundation for innovation and growth.