Introduction
This in-depth case study highlights the incredible story of an industry-leading company that pioneered the introduction of grinding wheel manufacturing to India back in 1941. The company has since diversified its product portfolio to include Abrasives, Ceramic Materials (Silicon Carbide and Performance Ceramics & Refractories), Performance Plastics, and ADFORS. The research explores the strategic programs of the company, including work content measurement using time study, capacity calculation, cycle time determination, manpower appraisal, and effective work distribution.
About the Client
The client, a pioneering icon in Indian manufacturing, started in 1941 as India's first company to manufacture grinding wheels. Through the decades, the company has evolved into a diversified industrial giant with international operations. Their portfolio ranges across Abrasives, Ceramic Materials (Silicon Carbide and Performance Ceramics & Refractories), Performance Plastics, and ADFORS. With its storied heritage of excellence in manufacturing, innovation, and quality, the client continues to be ahead of the curve in material technology and solutions. However, even a storied manufacturer has to keep changing to match up with contemporary efficiency standards. This project was an essential milestone in their quest for operational excellence.
Client Challenges
In spite of its vast product portfolio and large-scale manufacturing infrastructure, the client had some serious operational issues to contend with:
These problems were compromising productivity, manpower efficiency, and general output predictability. The client needed a systematic, data-based approach to rationalize operations, maximize workforce utilization, and benchmark plant capacity.
Project Objectives
Production Modeling India (PMI) was engaged with clearly defined objectives:
• Work Content Measurement using proven time study techniques.
• Plant Capacity Calculation to establish baseline and stretch targets.
• Cycle Time Standardization to enable better planning and execution.
• Manpower Optimization for improved labor utilization and reduced idle time.
• Balanced Work Distribution to reduce fatigue and streamline operations across all machines.
PMI’s Approach
PMI addressed this challenge with an end-to-end methodology customized to the client's unique production environment. The engagement was broken down into three core stages:
1. Data Collection
The initial step included a thorough on-site tour by the PMI team. The aim was to comprehend the operational process prior to initiating any analysis. High-definition video footage of the production operations on all 50 machines was taken. These tapes allowed a close look at every task and its corresponding time elements. Moreover, long interactions with floor-persons and supervisors contributed towards decoding the processes being measured. This ensured contextualization and congruence between observed and actual processes.
2. Estimation & Data Analysis
After gathering raw data, PMI started an intensive time study. Major activities were:
• Process Flow & Schematic Layout Designing: Plotting all vital paths through the manufacturing line.
• Elemental Detail Preparation: Application of time study techniques to decompose activities into measurable items.
• Work Content Estimation: Estimating time taken for every task, considering value-added as well as non-value-added (NVA) activities.
• Work Distribution Analysis: Designing man-machine charts for visualization of association between operators and machinery, allowing load balancing.
• Manpower Calculation: Calculating the right number of workers needed per shift according to set cycle times and production rates.
PMI also presented the client team to the Predetermined Motion Time System (PMTS) in order to make them learn and emulate time study methods on their own in the future.
3. Validation and Final Review
All the findings such as cycle times, capacity rates, and manpower suggestions, were checked with the representatives of the client to ensure alignment and acceptance by the important stakeholders. Care was taken to confirm the reliability of observed statistics against actual production output in real-time.
Particularly, Station 5C-010's material handling robot was found to be a chronic bottleneck, having the highest utilization and lowest availability in Zone 1. The other bottlenecks were 5C-030 and 5C-200, suggesting an upstream clustering of performance limitations. Line efficiency was computed at 93.4%, while machine availability throughout zones varied between 97% and almost 100%. The analysis also validated that the proposed buffers between downtime areas were adequate under existing operational conditions, avoiding cascading delays and preserving continuity of flow.
Driving Operational Excellence in Diversified Grinding Wheel Manufacturing Company
Key Results & Findings
After the analysis, some salient insights and suggestions were generated:
• Plant Efficiency Assessment: From statistics of 50 machines, the average current efficiency of the plant was determined to be 59.63%.
• Machine-Wise Benchmarking: 24 out of 50 machines were below average, and 26 were above it, demonstrating variation in operator effectiveness and equipment use.
• Future-State Projection: If overall plant efficiency could be increased to 75%, the distribution would be better, with 27 machines above the new average and 23 below it, showing a high potential for consistent process enhancement.
• Productivity Improvement: Current unit output per man per shift for 16-inch grinding wheels was 8 units. With the suggested optimizations, it could be brought to 11 units, thus showing a 37.5% improvement in productivity.
• Fatigue and NVA Reduction: Non-value-added operations and tasks contributing to fatigue were identified and removed by implementing improved task allocation and ergonomic enhancements.

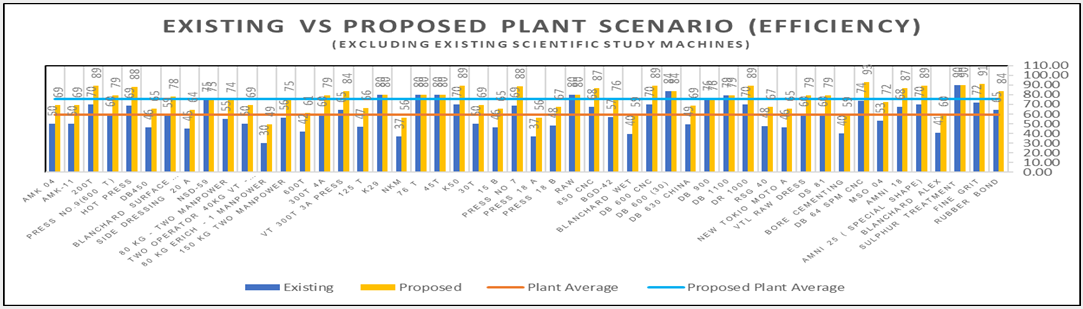
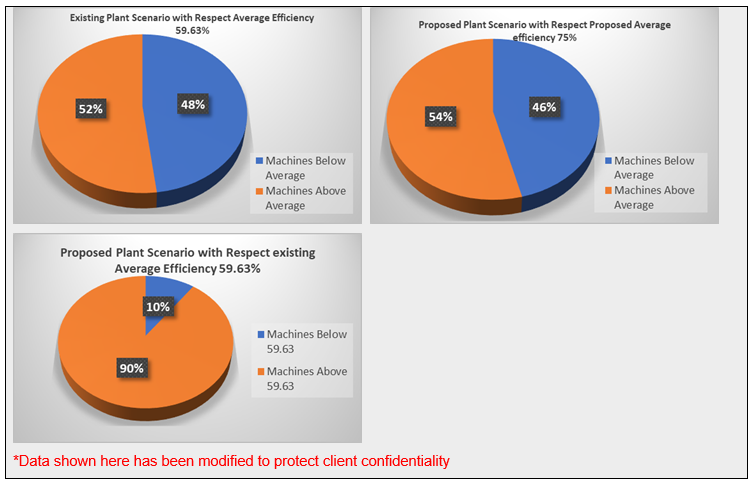
Conclusion
PMI’s structured intervention delivered quantifiable value to the client. By standardizing cycle times, calculating accurate manpower requirements, and optimizing resource deployment, the project laid a solid foundation for sustained productivity improvements. The use of video analysis and time study methods ensured objective evaluation, while client involvement throughout the process enabled knowledge transfer and long-term capability building.
From a productivity standpoint, the plant now has a roadmap to increase per-person output by nearly 40%, while balancing workloads and reducing inefficiencies. PMI’s engagement has helped this industry leader align its rich manufacturing legacy with the demands of a modern, performance-driven production environment.