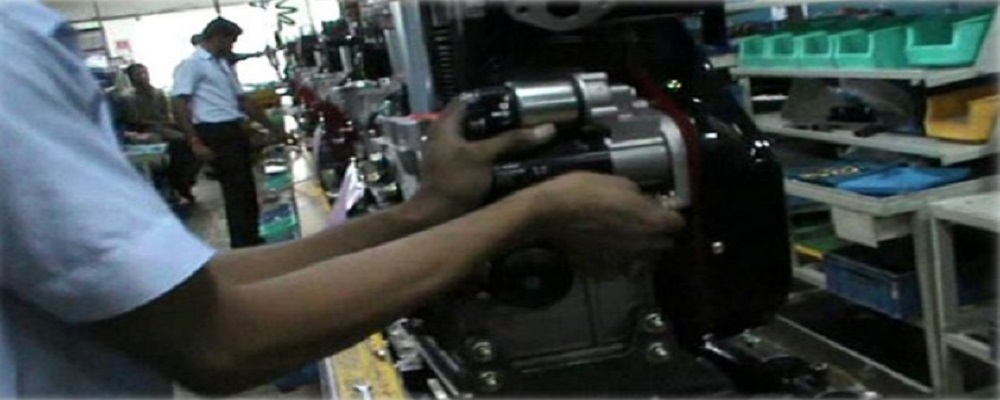
Introduction
In high-mix engine assembly environments, striking the right balance between manpower, productivity, and production pace can be a challenging feat. One of India’s leading manufacturers sought to address inefficiencies in their engine assembly shop, where multiple engine variants were built on a single line. With rising demand and high complexity, the company partnered with Production Modeling India (PMI) to conduct a detailed Work Content Estimation Study using PMTS (Predetermined Motion Time System) techniques.
The objective was clear—improve manpower utilization, define accurate work standards, and identify opportunities for productivity enhancement without compromising quality or flexibility.
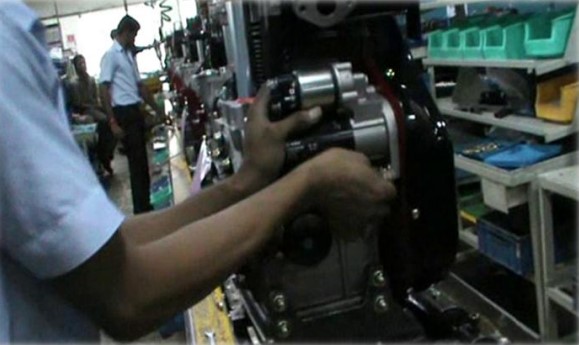
Client’s Challenge
• Underutilized manpower due to mix model variations
• Difficulty in achieving single TACT for all variants on one assembly line
• Lack of visibility into true potential capacity of the engine testing beds • Need to reduce overall manpower while maintaining output
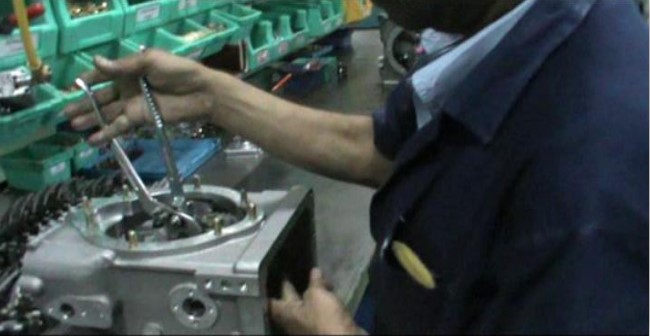
Work Content Estimation for Engine Assembly Line Using PMTS Study
PMI’s Approach
PMI initiated the study with extensive video recording of all assembly and testing activities. This was followed by a structured breakdown of tasks into elemental details, which were then analyzed using the PMTS technique to determine standard time values.
The study involved:
- Work content estimation for all assembly operations.
- Preparation of online-offline charts for engine testing activities.
- Manpower calculation for both multi-TACT and single TACT scenarios.
- Line balancing across engine sub-assembly, main assembly, and testing areas.
Findings and Recommendations
• Manpower utilization improved to nearly 90% with line balancing
• Overall manpower reduced from 59 to 53 while maintaining output
• Engine testing bed productivity improved by 30%, supported by optimized task sequencing
• Overall productivity across the plant improved by 31.9%.
• Single TACT was achieved for mix-model line, reducing production loss and improving flow.
• Clear work standards established for ongoing workforce planning and efficiency tracking.
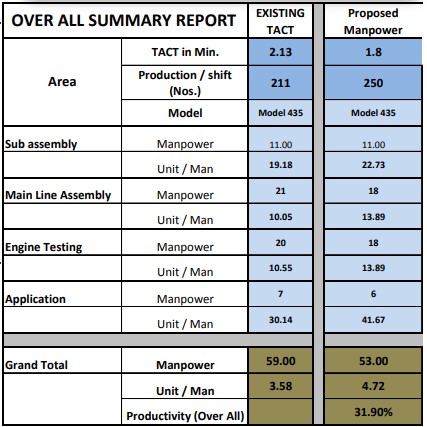
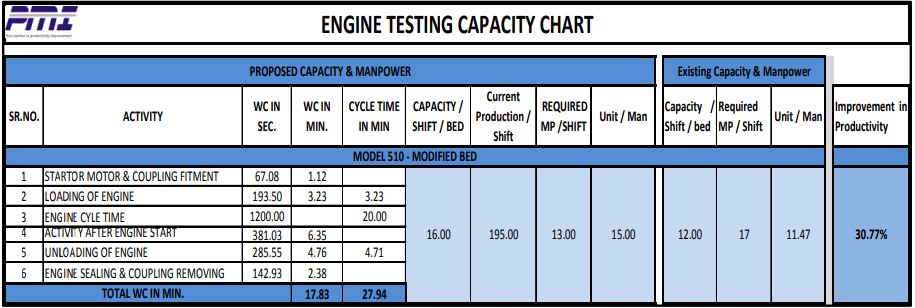
Conclusion
With PMI’s structured IE approach and PMTS-driven insights, the client successfully transitioned from fragmented task management to a lean, synchronized production model. The result: enhanced performance, measurable gains, and a production floor ready for scale.