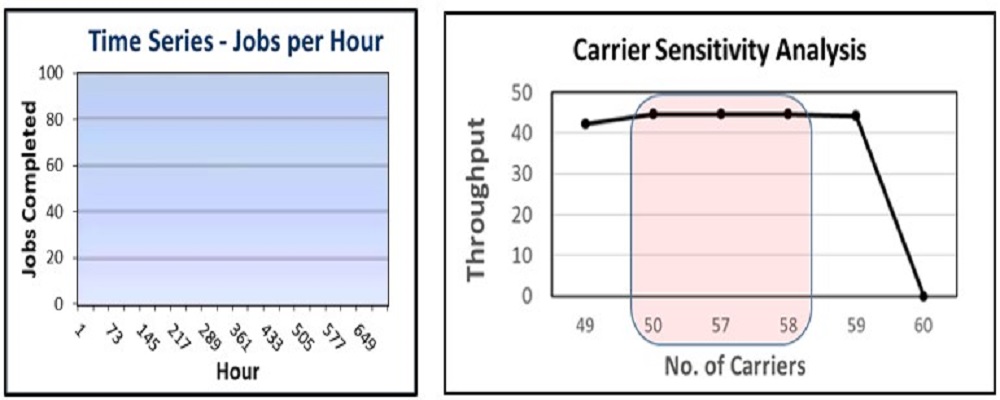
Introduction
It's never as easy as adding room or equipment to expand a production line. In the automotive manufacturing world, every operation is linked—and one holdup in one area can have a ripple effect throughout the plant. A globally recognized automaker, preparing to boost production, had a vision of bringing new body and paint facilities into their building. But with more complexity and pressure to sequence and quality, the firm needed answers before it could break ground.
That's where it brought in Production Modeling India (PMI) to model the planned plant layout and operations using AutoMOD, one of the top discrete-event simulation software. The objective: to confirm assumptions, detect bottlenecks, and streamline vehicle flow through the new body, paint, and final assembly facilities.
Client's Challenge
• Deciding on optimal buffer sizes and carrier numbers between the Body Shop, Paint Shop, and Final Assembly.
• Finding an efficient conveyor configuration and lane design to enhance vehicle routing.
• Minimizing purge operations in the paint shop spray booth due to mismatched body flow.
• Ensuring that painted bodies could be re-sequenced correctly before final assembly.
Given the intricacy of the system, especially with intermediate storage points like Body-In-White (BIW) and Painted Body Storage (PBS), a detailed simulation was the only way forward.
AutoMOD Simulation by PMI Identifies Bottlenecks and Unlocks Seamless Paint-to-Assembly Flow for Automotive Plant Expansion
PMI’s Simulation-Based Approach
PMI conducted a three-level simulation study, starting with individual shops and gradually integrating them into a plant-wide model.
PMI initially simulated the Body Shop, Paint Shop, and Final Assembly separately, detecting local inefficiencies and line-specific opportunities for improvement.
Subsequent to this, the individual models were integrated to represent entire vehicle flow with intermediate handling systems such as BIW and PBS.
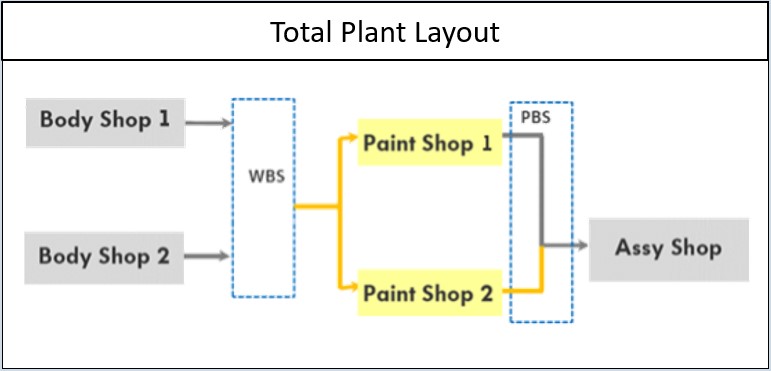
Key Findings & Recommendations
PMI’s simulation revealed that the main bottleneck in the system wasn’t in the new paint shop, it was in the chassis line of the final assembly, specifically tied to a limited buffer system and carrier availability.
Here’s what worked:
• Increasing the door loop conveyor capacity by 20 units significantly improved the system’s flow
• WBS (White Body Storage) and PBS (Painted Body Storage) adjustments with the suggested number of carriers supported smoother shop-to-shop handoffs
• Optimized routing rules between Body Shop and Paint Shop reduced purge activities in the spray booth
• New sequencing approaches prior to final assembly enabled the system to preserve production sequence, lessening rework and idle time
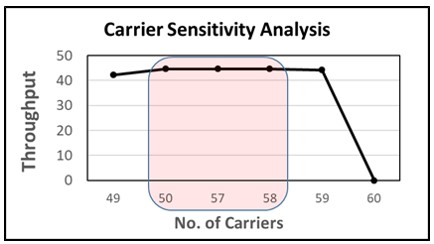
Conclusion
This simulation wasn't merely for validating expansion plans—it was future-proofing a production system. By seeing the effect of each carrier, buffer, and routing decision, PMI enabled the client to make decisions based on fact before spending on physical changes. With flow optimized and inefficiency cuts, the client is now better placed to deal with increasing demand without sacrificing quality or consistency.