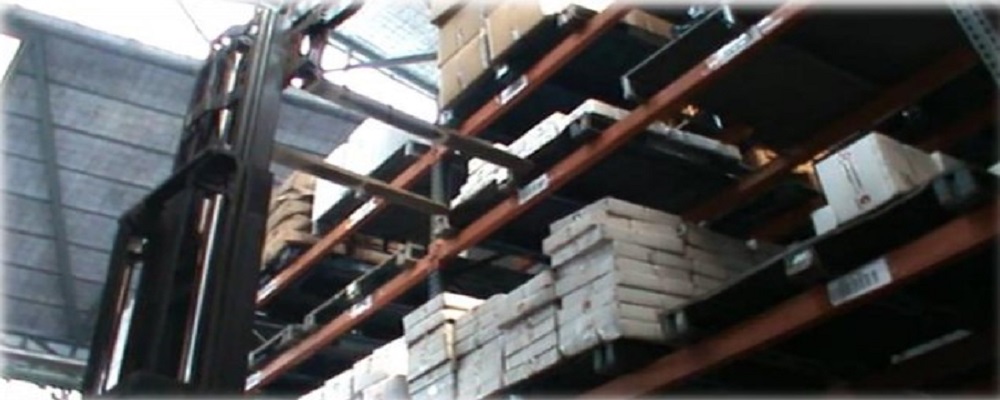
Introduction
In any manufacturing or production setup, the Stores department plays a vital but often under-optimized role. From receiving incoming goods to storing and issuing materials, each task involves a complex web of movement, handling, and coordination. A leading manufacturing firm realized that while their stores were operationally sound, they lacked data-backed clarity on whether the existing manpower was being effectively utilized. With efficiency becoming a strategic priority, the organization partnered with Production Modeling India (PMI) to conduct a Work Content Estimation and Manpower Study for their Stores Operations.
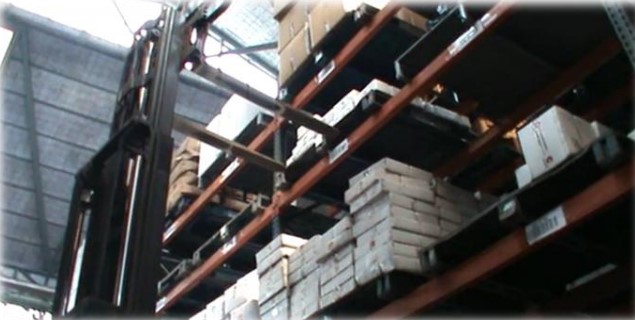
Client’s Challenge
• Unclear manpower requirements for varying production levels
• Suspected inefficiencies in resource utilization, especially during peak inventory movement
• Need for structured insights to support workforce planning
PMI Standardizes Stores Operations with 30% Productivity Gain and Data-Driven Manpower Planning – A Case Study
PMI’s Approach
PMI followed a phased and analytical approach:
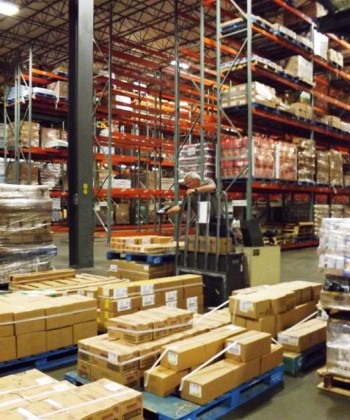
Defined key activities under Receiving, Storage, and Issuing operations.
Conducted on-site video shooting and direct observation of store operations across shifts.
Grouped materials based on size and packing type, as these directly impact handling time and effort.
Created an activity-wise time sheet using video-based time study methods, which became the foundation for manpower planning.
Activities were linked to their respective sections (receiving, storage, issuing), and manpower was calculated based on actual effort and task frequency.
Results & Impact
• A comprehensive work content database was developed, defining time standards for each activity.
• Manpower requirements were accurately calculated, helping avoid both overstaffing and understaffing.
• PMI recommended productivity improvements of 30% through better task allocation and workflow streamlining.
• The client now had a scalable framework for manpower planning, tied directly to production levels and store volumes.
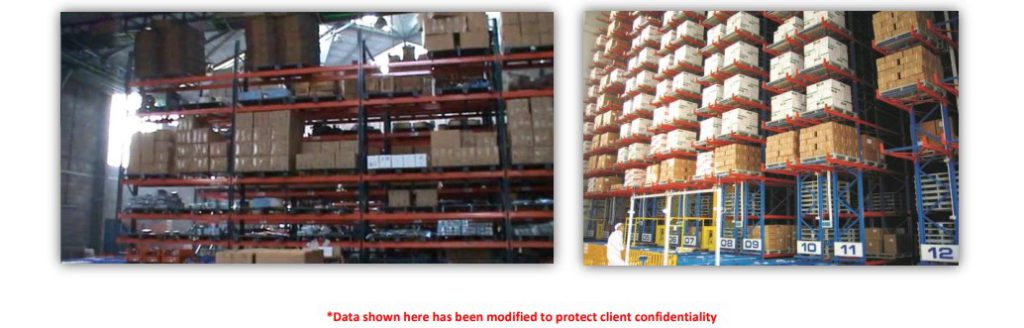
Conclusion
PMI’s work brought visibility, structure, and strategic clarity to what was previously an instinct-driven function. With objective time standards and smart manpower insights, the Stores department is now better aligned with the company’s operational goals.