
Introduction
In a dynamic energy sector, the call for clean technologies such as fuel cells is increasing. But this boom introduces new manufacturing complexities, demanding delivery schedules, changing customer requirements, and the necessity for ongoing process innovation. A prominent fuel cell manufacturer, seeking to improve throughput and operational flexibility, approached Production Modeling India (PMI) to help them test system-level strategies in a risk-free simulation environment before real-world implementation.
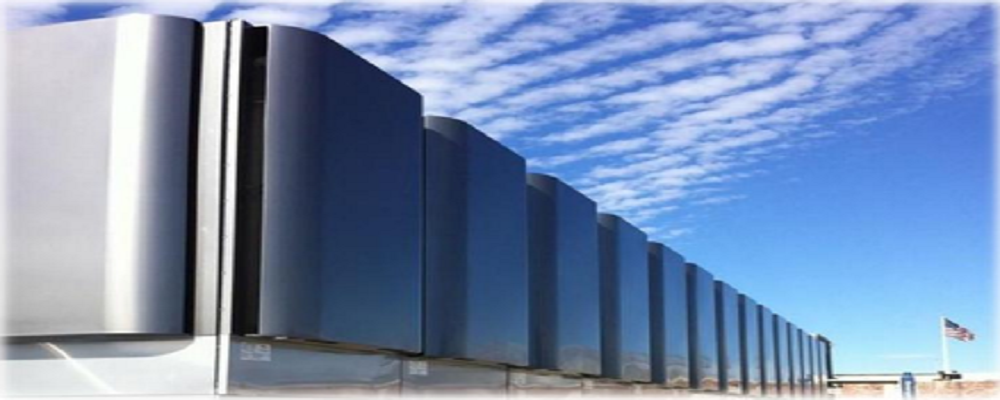
Client’s Challenge
- Develop and validate new operational strategies without disrupting ongoing production.
- Identify bottlenecks and capacity limitations in a complex, multi-stage manufacturing line.
- Understand the robustness of chosen strategies under fluctuating market and product demand.
- Determine optimal buffer sizes and inventory positioning to reduce wait times and improve flow.

From Bottlenecks to Breakthroughs: Simulation-Driven Planning in Fuel Cell Manufacturing - A Case Study
PMI’s Approach
PMI utilized a methodical simulation approach to create a reliable decision-making tool for the client:
Data Analysis and 2D Model Development
The manufacturing line was modeled using real-time production data to mirror existing operations.
Model Verification & Validation
The simulation was refined to accurately reflect throughput, work-in-progress (WIP), and downtime scenarios.
Bottleneck Identification
Using WIP accumulation and Time-In-State (TIS) metrics, the Sintering Oven was identified as the first constraint, followed by the Inspection and Glue Station.
What-if Scenarios & Sensitivity Analysis
Capacity changes at bottlenecks and buffer modifications were tested to measure impact on weekly throughput.
Throughput Roadmap Creation
Based on simulation results, PMI devised a Throughput Improvement Roadmap, ranking strategies by effectiveness and feasibility.
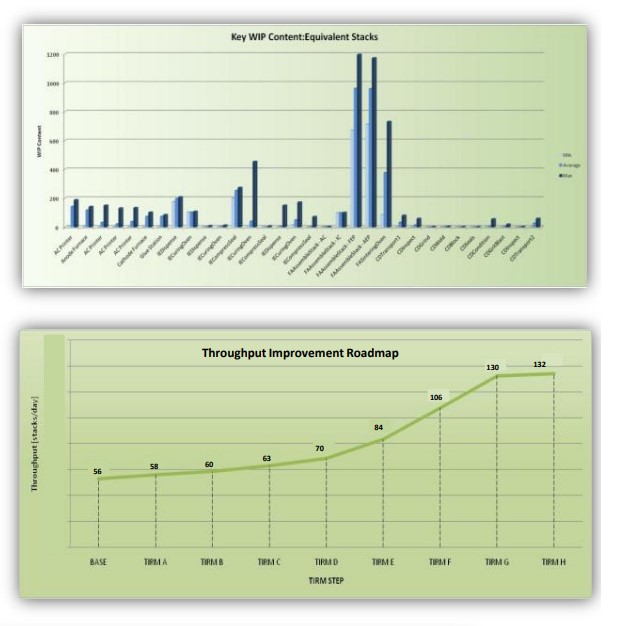
Findings & Recommendations
• The plant could produce a maximum of 310 fuel cell stacks per week under current constraints.
• By increasing capacity at key bottlenecks, throughput gains were achieved across multiple simulations.
• Buffer analysis revealed the optimal number of boats needed per furnace batch.
• The best-performing strategy was selected for real-world implementation, ensuring higher reliability with minimal risk.
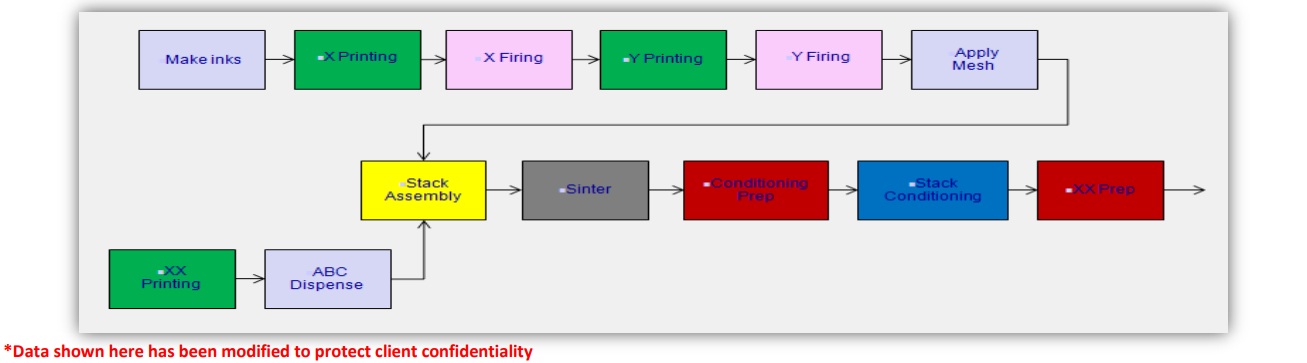
From Bottlenecks to Breakthroughs: Simulation-Driven Planning in Fuel Cell Manufacturing - A Case Study
Conclusion
Simulation empowered the client to test complex ideas in a virtual world, saving time, cost, and uncertainty, paving the way for smarter, faster, and safer decisions in fuel cell manufacturing.