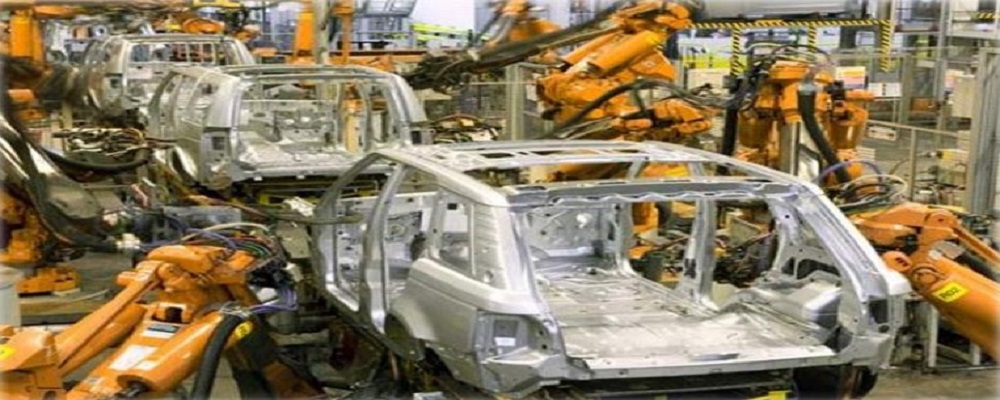
Introduction
For a Greenfield automotive facility gearing up to meet aggressive production targets, streamlined material movement is not just important—it’s mission-critical. The client, a leading automobile manufacturer, sought to ensure that the Blanking and Stamping processes would not become bottlenecks for downstream operations, especially at the Body Shop.
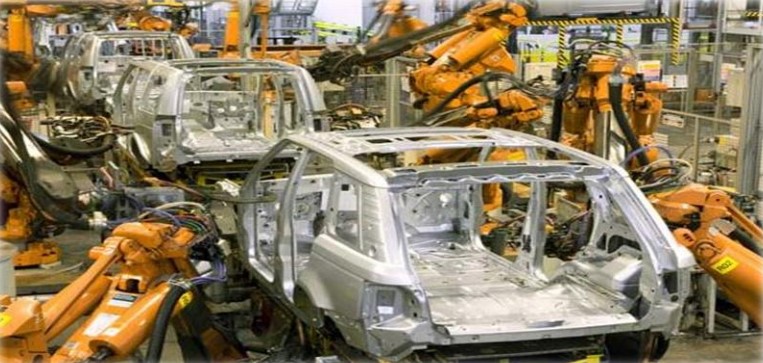
With high throughput expectations and complex movement patterns involving forklifts and cranes, the challenge was to evaluate the material handling equipment (MHE) requirements, identify congestion risks, and determine the optimal operational configuration. PMI was brought in to conduct a comprehensive material movement simulation study to unlock efficiency in these critical upstream operations.
Client’s Challenge
- Ensure Blanking and Stamping operations do not hinder the overall body shop throughput.
- Determine optimum MHE (forklift) requirements.
- Understand how crane movements and die changeover times influence material flow and line performance.
- Identify and eliminate congestion hotspots caused by forklift movement.
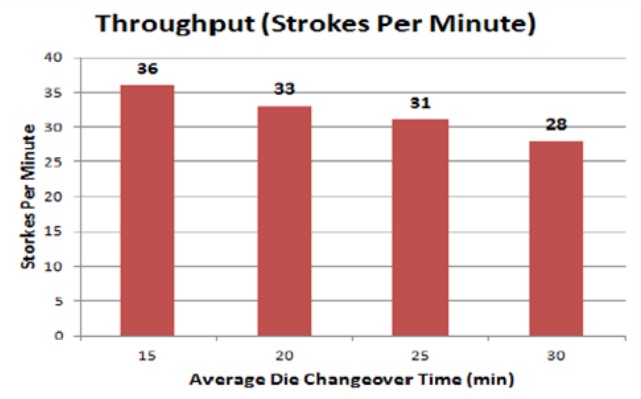
How PMI Reduced Material Handling Equipment Needs by 30% in a Greenfield Automotive Plant - A Case Study
PMI’s Approach
PMI took a simulation-driven approach using plant layout data and operational inputs to build and validate a detailed material flow model:
Data Analysis and Baseline Verification
Mapped all activities between Blanking, Stamping, and intermediate storage, validating the baseline operational assumptions.
Impact of Forklift Utilization
Analyzed how the number of forklifts influenced material availability at stamping lines, congestion at storage areas, and underutilization across zones.
Die Changeover Analysis
Modeled the impact of crane-based die changes on production loss and tested different changeover time scenarios.
Congestion Mapping
Captured and quantified bottlenecks in forklift traffic, particularly at stamping storage and blanking line ends.
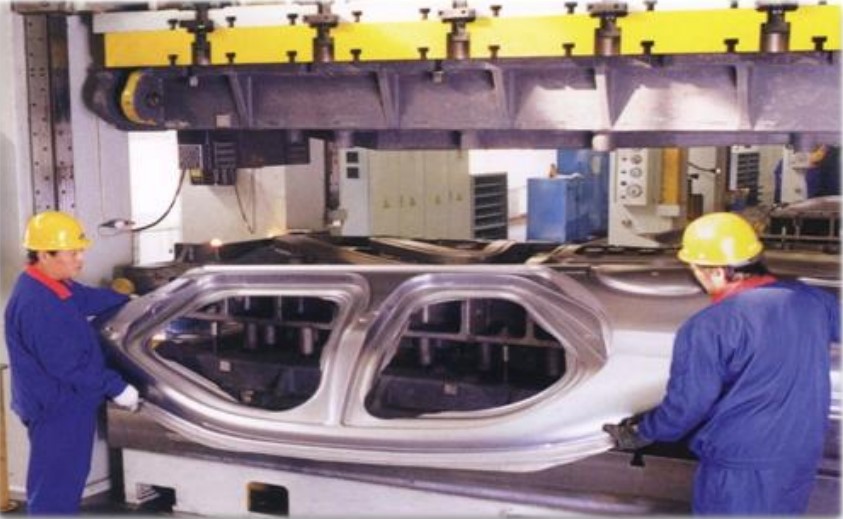
Findings & Recommendations
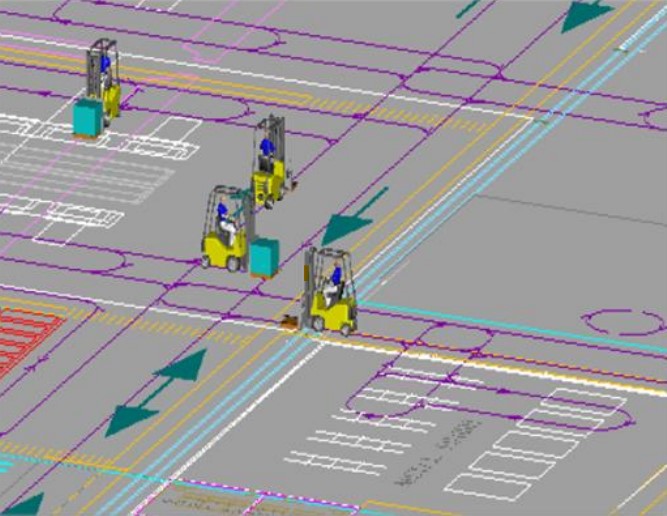
• Congestion at the stamping storage area was found to reduce production efficiency due to overlapping forklift traffic.
• Forklifts at the end of the blanking line were underutilized, contributing to operational inefficiency.
• PMI proposed doubling the pallet load per forklift trip, leading to smoother traffic flow and reduced congestion.
• The optimized movement resulted in a 30% reduction in MHE requirement, minimizing capital and operational expenditure.
• 30 minutes was established as the maximum permissible die changeover time to avoid disrupting downstream throughput.
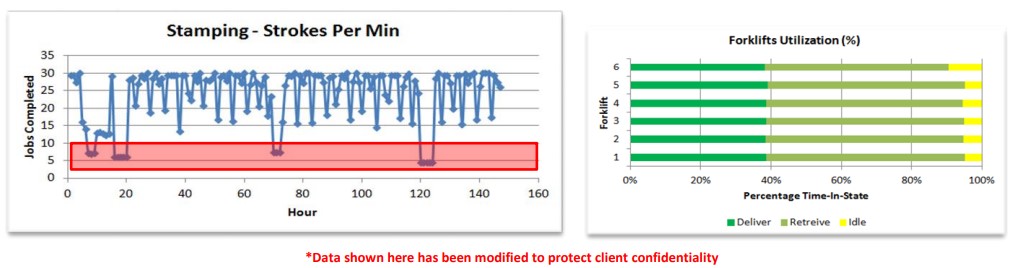
How PMI Reduced Material Handling Equipment Needs by 30% in a Greenfield Automotive Plant - A Case Study
Conclusion
Through meticulous simulation and data-backed analysis, PMI helped the client transform their material movement strategy, ensuring leaner operations, reduced costs, and a clear path to scalable production in the new facility.