Streamlined and Effective Jig and Fixture Design Solutions
In automotive manufacturing, the Body in White (BIW) stage involves welding together sheet metal components to form the vehicle's main structure. Various welding techniques, including robotic welding, laser brazing, MIG welding, MAG welding, spot welding, and riveting, are used with the assistance of jigs and fixtures to ensure precise alignment of all components. Once the BIW process is finished, the vehicle can undergo painting and the installation of major components such as the engine, chassis, and trim.
Experience the expertise of our BIW fixture design experts. With our comprehensive robotic simulation services, we deliver designs that optimize efficiency and ensure exceptional reliability.
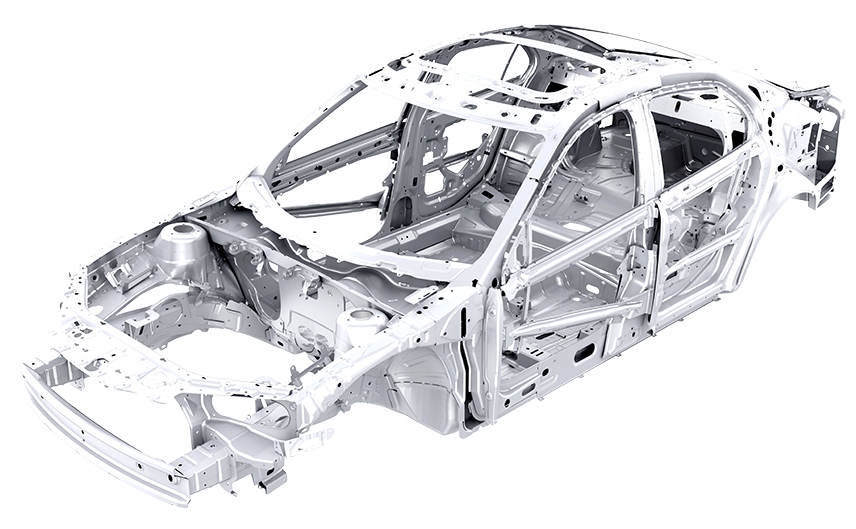
Body in White Design and Detailing Services
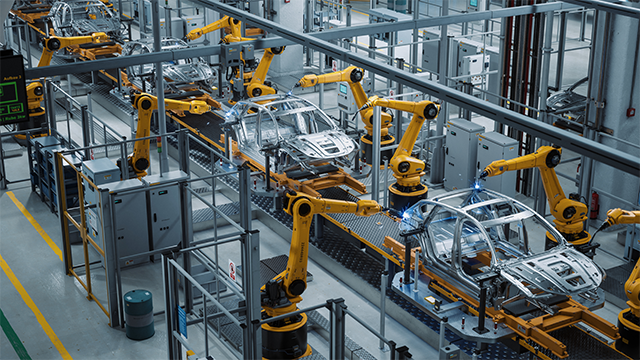
- Complete automotive body shell welding fixtures
- Geo Station Re-Spot
- Prototype and series production welding fixture design
- Framing stations for side body
- Checking and Setting fixture design
- Hemming fixture design
- Weld Gun foul analysis
- Robotic Gripper customization
- 2D drafting, detailing, and 3D concept designing
- Bill of material generating
- Equipment for assembly
- Equipment for process confirmation
- Conveyors and shuttle systems
Related Service: Robotics Simulation for BIW
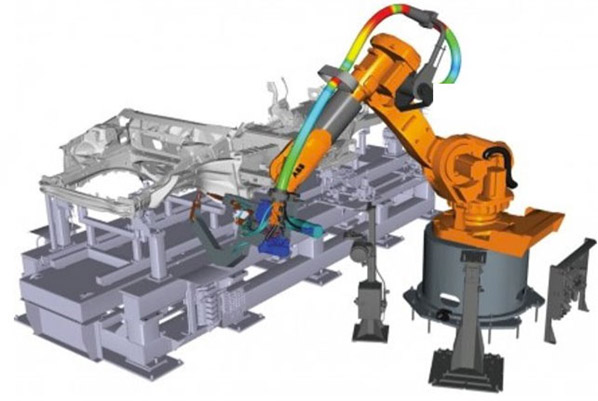
PMI is a provider of robotics simulation solutions tailored for the automotive industry. Our services are crafted to enhance the Body in White process, empowering manufacturers, OEMs, and suppliers. Our services help to streamline operations, minimize cycle times, and boost production efficiency. Featuring an extensive suite of user-friendly software solutions, including robot path planning, motion analysis, collision detection, and error handling, we seamlessly integrate with existing systems for hassle-free implementation.
Robotics simulation enhances the effectiveness of jigs and fixtures in Body in White automotive manufacturing. It enables engineers to test and refine designs prior to physical construction, resulting in cost savings and increased efficiency. By identifying potential issues early on and analyzing structural integrity, simulation facilitates the development of more effective and innovative solutions.
BIW Fixture Design Process
- Discovery: Collaborate closely with the client's team to comprehend their specific needs and ensure our jig and fixture designs align perfectly with their requirements.
- Preliminary Draft: Meticulously follow specifications to create precise and efficient jig and fixture designs, facilitating seamless draft reviews.
- Visualize in 3D: Transforming the 2D drafts into immersive 3D visualizations, allowing clients to examine mechanical parts and understand system functionality in intricate detail.
- Quality Control: Conduct comprehensive qualitative analysis of the fixture design, meticulously verifying compliance with requirements. Additionally, provide cost estimates, fabrication details, and a comprehensive bill of materials.
- Deliverables: Once the design execution is verified, securely deliver the final deliverables through our reliable FTP servers.
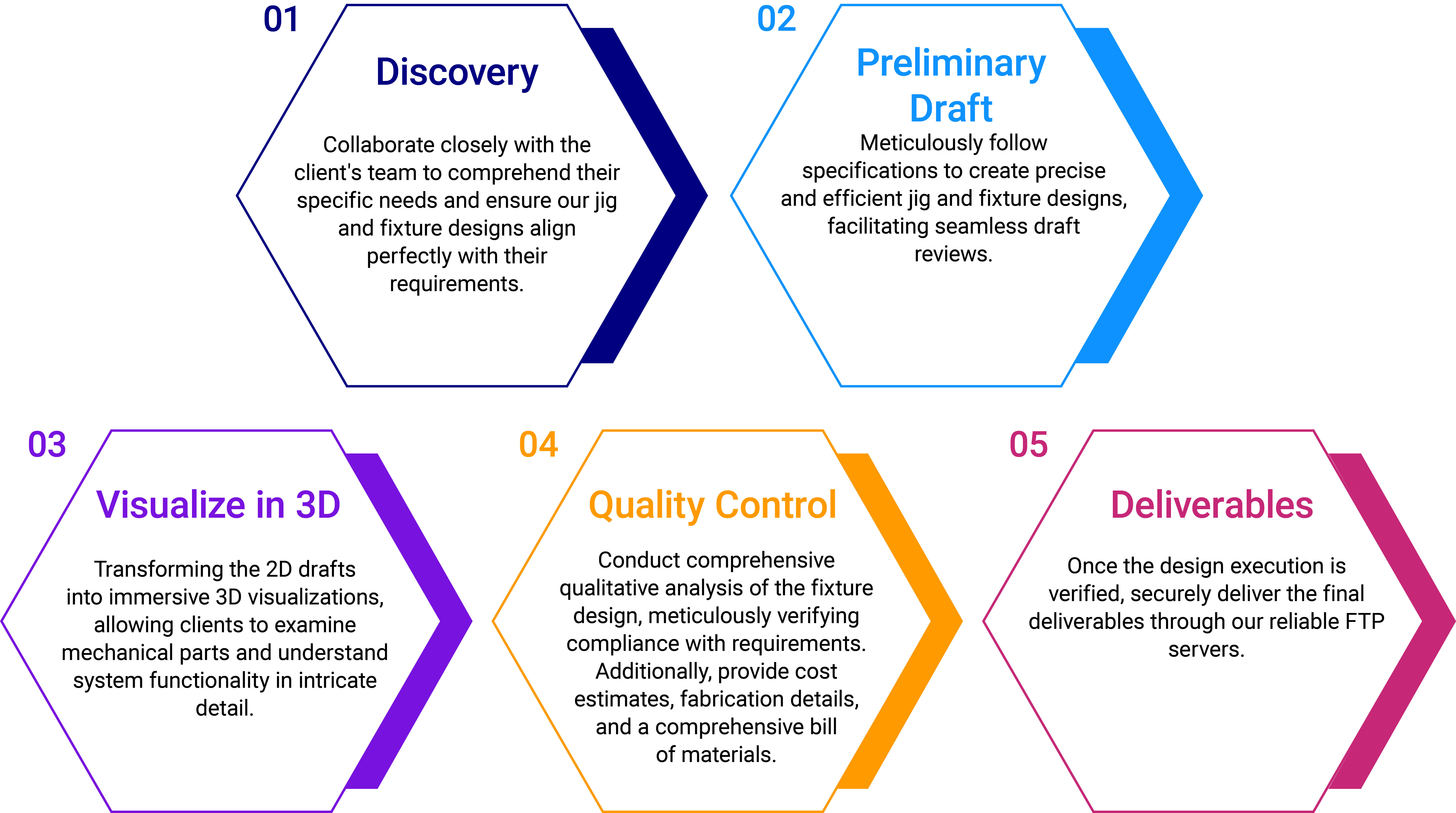
Workflow and Deliverables
Workflow Design
- Assembly Sequence Charts
- Datum Sheets
- Feasibility study
- Plant Process study
- Standards & Layout
- Panel Build-Up:
- Cycle time study
- Ergonomic Study
- Location & Clamp plan
- Sealer Sheet
- Weld Data Sheets
- Weld Force Study
- Weld guns selection
- Weld spot distribution
Tooling Support for CAD Mechanical Design
- Buffer Storage bins and racks.
- Checking fixtures.
- Geo Fixtures
- Geo Grippers
- Gripper docking stations
- Handling Grippers
- Panel Deposits
- Re-spot Fixtures
Technical Drawings
- Detail & Assembly drawings
- Flame cut drawings
- Generating BOM
- Machining Drawings
- NC's Body positioning
- Pneumatic Circuit diagram
- Technical Documentation as per OEM standards
- Unit Assembly Layout
CAD Software
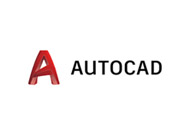
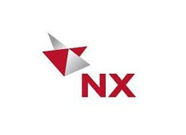
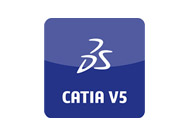
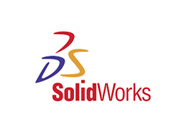
Simulation Software
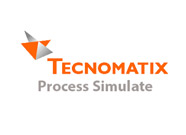
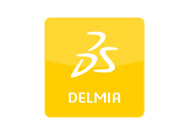
PMC Engineering Design Advantages
Quality Assurance (QA)
- Experienced team of engineers and designers with extensive industry expertise
- Internationally recognized and certified processes ensure top-quality deliverables
- In-depth knowledge of global regulations and standards to ensure compliance
- Comprehensive engineering services tailored to meet diverse requirements
- An abundance of talented resources with diverse skill sets
- Flexible resource allocation to accommodate ad-hoc demands
Versatility
- Optimized business processes
- Adaptable schedules
- Easily expandable resources
- Cost-effective approaches
- Committed customer support
Collaboration
- Exceptional data management capabilities
- Strong and reliable technology governance
- Smooth and efficient information sharing
- Expert-level IT support and assistance
Growth Potential
- Enhanced operational efficiency in back-office processes
- Adaptability to diverse client cultures for effective collaboration
- Substantial cost savings in engineering and technology, up to 20-30%
- Enabling in-house teams to prioritize core business development
- Expanded bidding capacity for clients with lower engineering costs and timely deliveries
- Establishment of dependable and productive partnerships
Our Team
Our skilled team of engineers and designers excel in developing fixtures that are optimized for superior efficiency, accuracy, and reliability. By leveraging simulation techniques, we guarantee that our fixtures meet precise specifications. Our comprehensive robotic simulation services provide in-depth analysis, optimizing robotic systems for optimal speed, accuracy, and safety. Trust us to deliver your BIW Fixture & Tooling Design and Robotic Simulation projects punctually and within budget.
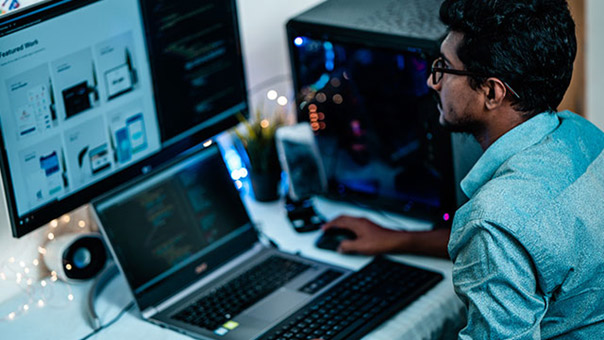
Frequently Asked Questions for BIW
Speak with one of our Jig and Fixture Design Experts!
Send a message to our team by filling out the form below. Describe your project, ask questions, or even request a bid.
An expert from our team will be in touch with you within one business day!
Want to schedule a time to speak with one of our representatives NOW?